Veneering is an excellent way for DIYers to work with highly-figured domestic and exotic woods that are too expensive for most of us to purchase as solid boards.
Windsor Plywood, for example, has a selection of hardwood lumber that retails for $5 per board foot of maple, $8 per board foot of walnut and $26 per board foot of zebra wood.
For small projects, such as jewelry boxes, Lee Valley sells a large pizza box filled with 20 species of veneer from throughout the world for about $60. Larger sizes and quantities are available from Oakwood Veneer Company in Michigan that sells up to 5-by-12-foot sheets with a paper backer to prevent splitting or bubbling when applied. This is a very reliable company with over 320 species of wood veneer in stock, shipped to most large cities in Canada in one to three days.
The only problem is with the Canadian loonie currently at a new low compared to the American dollar, you will pay a premium by ordering from Oakwood. In Canada, A&M Wood Specialty of Cambridge, Ontario, sells and ships well over 100 decorative veneers, most available in random sizes from 5-to-8-inches wide and about 10-feet long. These veneers do not have a backer (backed products are available on request) and, as a result, are much less expensive. For example, paper-backed sheets of quartered zebra wood from Oakwood cost over US $9 US per square foot. The same product without a backing from Cambridge costs $3.25 Cdn per square foot.
One of my favourite veneers is macassar ebony, cut from trees that grow on the islands of Indonesia. While the tree is not endangered, political strife and difficulty accessing the wood have contributed to its high price and rarity as a solid timber. The veneer, however, a lovely combination of black, reddish brown and deep yellow stripes, is available on the Internet from Veneer Supplies.com.
Veneer is generally sold in flitches, piles of eight sheets that are cut consecutively from the same log (also called a flitch) so their figure does not vary when they are book or slip matched on a large surface such as a sheet of MDF. For small boxes, book matching, in which one sheet of veneer is flipped so that it will create a mirror image of the other, is a good method to create a dramatic pattern on the lid. Veneers with a straight figure are generally slip matched, placed side-by-side on the substrate without flipping the sheets.
The best substrate for veneer is MDF because it does not move seasonally, unlike pine or other softwoods that were traditionally used by ebenistes, a French name for cabinetmakers who worked with precious woods and veneers. If you examine a finely veneered piece of furniture from the Art Deco period of the 1920s, it’s likely the veneer will have cracked because of the movement of the wood substrate. Another advantage of MDF is that it has a perfectly smooth surface, allowing a good bond between the veneer and the substrate.
For a small jewelry box, quarter-inch thick MDF is suitable. There are several methods to apply the veneer, the traditional one being to brush hot hide glue onto the substrate, followed by the placement of the veneer and several smoothing passes with a veneer hammer. The word hammer is misleading as the tool actually is a piece of wood (the head) with a handle in which a long, flat piece of non-ferrous metal is embedded. The edge of the metal protrudes about a quarter inch from the head and is used somewhat like a squeegee to force out excess glue and press the veneer tightly to the substrate.
I don’t recommend this technique as in my experience hide glue smells bad, has a very low initial tack and seeps through to the surface of the veneer, creating an unsightly mess that must be removed with a cabinet scraper.
The second method, mechanical veneering, yields better results but requires a homemade press. It can be made of two sheets of plywood and wood clamps, between which the piece being veneered is squeezed by tightening the clamps. Place a sheet of wax paper over the veneer so it does not adhere to the plywood while under pressure. (I know of one young fellow who drove a wheel of his car over the veneer and plywood sandwich to apply sufficient pressure to weld the veneer and substrate together.) Wait 24-hours before releasing the pressure to be sure that the glue has dried completely, whether it is yellow, white, two-part urea-formaldehyde or epoxy.
The method I prefer for veneering small surfaces requires good quality contact cement that is brushed onto the MDF substrate and the backside of the veneer. When the glue loses its gloss, usually after 20-minutes at room temperature, place a piece of thin plywood over the substrate, align the veneer and then slowly move the plywood along the substrate while pressing the veneer to the glued substrate with a brayer, veneer hammer or smooth scrap of hardwood.
On larger surfaces, this method can result in bubbles trapped between the veneer and the substrate. They only can be removed by slicing open the bubbles with a sharp knife and injecting fresh glue into the opening, and then clamping a piece of wood covered with wax paper over the mend.
For big surfaces, such as a four-by-eight-foot sheet of three-quarter-inch MDF, the ideal tool is a vacuum press. These can be purchased from companies on the Internet or made by hand with a fractional horsepower motor, a small vacuum pump (try Princess Auto) and a large vinyl bag. The bag should be at least 10-feet long and nine-feet wide to accommodate large sheets of MDF. The seams can be glued by cleaning the vinyl with acetone and then using a contact spray adhesive to seal them.
Vacuum veneering can be fun, but a press requires a lot of space that may not be available in a DIY shop. I recommend starting out by experimenting with a small project such as a box covered with a highly-figured veneer held in place with contact cement.
For detailed information on all the techniques mentioned in this article, see The Veneering Book by David Shath Square, published by the Taunton Press of Connecticut, Massachusetts. It is available on Amazon.

Real Estate News
Oct 30 2014 Issue
- Local commercial real estate market maintains its stability in all sectors
- Charlie Chaplin — played the “Inebriate” on stage
- House hunting in a buyers’ market
- Two stock market theories
- Happenings on the November calendar
- Big and small wood veneer projects
- Local commercial real estate market maintains its stability in all sectors
- Charlie Chaplin — played the “Inebriate” on stage
- House hunting in a buyers’ market
- Two stock market theories
- When German is your mother tongue
- Happenings on the November calendar
- Big and small wood veneer projects
Search issues by word/phrase…
Or browse issues by year/month…
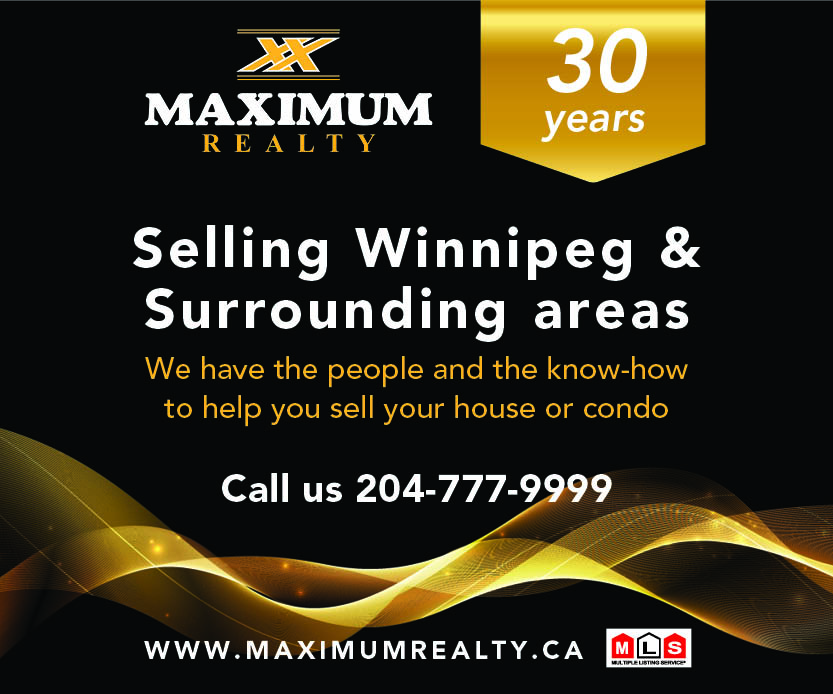